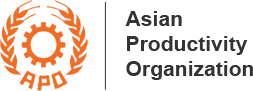
Select Page
Total quality management (TQM) is a management strategy based on the participation of all involved in operations and aimed at long-term success through customer satisfaction and benefits to all levels of the organization and society. However, successful TQM implementation requires focused efforts. Recognizing the importance of adopting TQM in member countries, especially by SMEs, the Asian Productivity Organization (APO) recently conducted a workshop on Management Consultancy on Total Quality Management in Nadi, Fiji, from 24 to 28 April 2017.
The workshop was designed to enhance the competency of consultants of NPOs or similar institutions in the area of management consultancy on TQM applications. It also aimed to equip participants with in-depth knowledge and know-how in providing management consultancy services on TQM and to discuss the issues and challenges of quality management practices in embracing Industry 4.0. The workshop was structured to share the best practices of TQM implementation and possible integration with other productivity improvement initiatives, including international standards and certification.
A total of 23 participants and two observers from 15 member countries attended the workshop that was organized in cooperation with Fiji National University, with resource persons from Japan, Malaysia, and New Zealand providing expertise and sharing case studies of TQM implementation. The workshop was inaugurated by APO Director for Fiji Salaseini Daunibuna, who is also Permanent Secretary, Ministry of Employment and Productivity. The opening ceremony was also attended by National Training & Productivity Centre Acting Director Peni Aore Taoi and Deputy Director Sachin Deo.
Japanese Resource Person Yuki Tanno advised participants to focus on the seven TQM steps or the quality circle story, which are mainly based on the plan-do-check-act cycle and similar to the define, measure, analyze, improve, and control, commonly known as the DMAIC core tool of Six Sigma, when introducing TQM in SMEs. He emphasized the importance of explaining basic productivity concepts and eliminating non-value-added processes when conducting SME consultancy. The “3 Ms of management, mindset, and motivation” were elements that SMEs could focus on when successfully implementing TQM, Tanno continued, which would allow them to celebrate every stage of achievement to enhance employee motivation.
Resource Person from Malaysia Shaharum spoke on the impact of Industry 4.0 on TQM initiatives. He explained that quality management in the future would focus more on the maximization of value, collaboration, “we” instead of “you,” improvements, and business innovation. In providing consultancy and training to make changes possible in SMEs, Shaharum suggested that such services be delivered using simple, flexible methods. Taking their capabilities into account, consultants should guide SMEs based on current needs and issues. He stressed that companies should view TQM as part of the quality journey involving continuous improvement.
The “3 Es,” signifying “engage, enlighten, and excel,” were introduced by Resource Person Michael Voss of New Zealand as steps organizations could take to achieve excellence. Speaking on TQM sustainability, Voss recommended the business excellence framework as one method companies could adopt over the long term. Sharing his experience as a management consultant in New Zealand, he advised participants to act as facilitators and translators when providing services to clients.
During the workshop, participants also visited Fiji Electricity Authority (FEA) to observe its quality management practices and initiatives. FEA employs almost 800 staff and won the Fiji President’s Quality Award in 2012. Among its quality initiatives and practices, the company is aggressively promoting quality control circles (QCCs). Currently, 67% of employees are involved, with 50 active QCCs. The overall group winner will represent FEA in the next International Exposition of Team Excellence Symposium in Singapore, and the organization plans to compete in the American Society for Quality International Team Excellence Awards in the USA later this year.