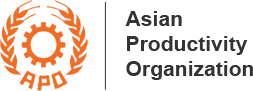
Select Page
In efforts to build member countries’ capacity to adopt the Fourth Industrial Revolution, including senior government officials involved in industrial policy formulation and representatives of industrial associations, the Asian Productivity Organization (APO) organized a mission to Japan, 6–9 March 2018. The Study Mission on Productivity Enhancement through Applications of Industry 4.0 in Japan was attended by 20 participants from APO member countries and one from Myanmar.
Participants gained firsthand knowledge of how different organizations in Japan use advanced IT applications and devices as well as artificial intelligence (AI) and robotics to improve productivity and process efficiency. They also learned about Japan’s Society 5.0 initiative and how the government and industry work together to dovetail the concept with Industry 4.0 to meet the challenges of an aging workforce.
Fujitsu I-Network Systems Limited staff demonstrating how Internet of Things technology enhances productivity in manufacturing processes, Yamanashi prefecture, 7 March 2018.
In welcoming mission members, APO Secretariat Industry Department Director Hikaru Horiguchi described Industry 4.0 as “exposing all countries to enormous challenges, such as the need to adapt in timely ways to changes, upgrade technological capabilities, and close gaps, while transforming the workforce.” “At the same time, this ICT-based industrial revolution will level the playing field and offer great opportunities for countries to leapfrog to the front line of development with the benefits of increased productivity, reduced waste, and more sustainable patterns of production and consumption,” he continued.
Horiguchi said that the study mission was part of assistance to help all APO members to embrace Industry 4.0 through a step-by-step approach. “This mission provides participants with opportunities to learn from Japan’s efforts to promote Society 5.0 and relevant industries to determine how they may be applicable in their countries,” he stated.
The study mission, funded by a special cash grant from the Government of Japan, included classroom presentations by APO international experts from Germany and Japan and site visits to FANUC Corporation, Fujitsu I-Network Systems Limited, and DMG Mori Seiki Co. Limited. Those visits showed how smart manufacturing functions as a preventive maintenance tool and how deep-learning applications are being adopted for AI and robot training. Participants also observed the Internet of Things utilized in the factory environment and how it supports data collection for informed decision making.