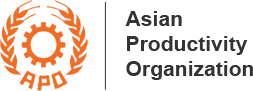
Select Page
In 2023, the Mongolian Productivity Organization (MPO) partnered with the APO to enhance KM in key sectors, selecting Erdenet Mining Corporation (EMC) as a demonstration company. EMC, operating the world’s fourth-largest copper mine and a major contributor to Mongolia’s GDP, faced challenges in knowledge retention, innovation, and productivity among its young and inexperienced workforce. Approximately 70% of ECM employees are between the ages of 20 to 40, with 51% of them having less than 10 years of experience, despite the company’s accumulation of knowledge over 50 years of development (Figure 1).
![]() |
![]() |
Figure 1. Breakdown of EMC employee demographics reported prior to the start of the project.
The project was divided into four phases: introducing KM; developing goals; assessing areas for intervention; and designing a roadmap to incorporate KM frameworks into operations. The final phase focused on measuring achievements and disseminating the know-how and successes.
To address these challenges, EMC identified the need to share knowledge within the workplace and facilitate the transfer of experience to employees. This initiative focused on several key actions:
• Bringing documented information closer to knowledge seekers;
• Enhancing productivity by ensuring ergonomic work environments for employees;
• Developing a comprehensive database for effective management and utilization of documented information and resources; and
• Systematically distributing and documenting the knowledge gained through experience to benefit the entire workforce.
EMC launched a KM project on “the Knowledge-sharing Workplace” led by the Suld Quality Circle team, for which the staff repair room was transformed into a micro-learning hub. Lighting and sliding boards were installed on the walls, showcasing technical diagrams, breakdowns, and parts of essential equipment for repair. Manuals and instructional materials were prominently displayed and regularly updated to ensure accessibility for all employees. “Behind this information board, there is a shelf. This information board for the 40-ton Belaz truck spare parts can give guidance on assembling, dismantling, or ordering spare parts, which saves time by allowing us to get all this necessary information from this single point in our workplace without the need to look for a manual,” explained Budbazar B., a specialist from the EMC auto transportation unit.
![]() |
![]() |
Suld team preparing displays and materials for sharing workplace knowledge.
The project involved a series of strategic actions designed to improve operational knowledge and reduce downtime. Data on the breakdowns and operational inefficiencies of crusher components were meticulously collected and analyzed. To enhance knowledge transfer, targeted training sessions were organized, and a mentor-mentee system was implemented, ensuring that the depth of technical know-how was deepened across the workforce.
After five months of implementation, significant progress was achieved: three sections were added to the LED information board, 11 sections to the sliding information board, and labeling in 20 locations by employees; and four types of brochures and three videos with voiceovers and subtitles on occupational health and safety were created.
![]() |
![]() |
The impacts were profound, evident in the increased technical readiness ratio and heightened employee engagement in threat detection and reporting (Figures 2 and 3), leading to a decrease in threats. As a result, employee satisfaction levels have seen a notable increase. Tsogtgerel G., General Engineer, emphasized the broader impact of these improvements: “By sharing skills and knowledge from one employee to another, we will ensure that the organization’s operations will never stop due to depending on a single employee.”
![]() |
![]() |
Figures 2 and 3. Technical readiness index by quarter and number of hazards reported for risk management.
Reflecting on the project’s success, Productivity Expert Urantsetseg L. of the Strategic Development Department noted, “We can see that putting this project into action was successful in teaching us how to manage knowledge inside the organization and how to boost productivity using effective learning strategies.” The project’s success was underpinned by strong management support, as Oktyabr B., Head of the Strategic Development Department, highlighted: “The management team of Erdenet Mining Corporation prioritized and gave full support for implementing this knowledge management project. We were able to effectively finish the project by appointing a working group, project teams, units, and implementation plans for each subproject with the General Director’s order.”
The EMC case study demonstrates how the APO assists in expanding capacity building and promoting best practices, thereby contributing significantly to the centrality of productivity within organizations, which can be emulated by other enterprises. These efforts exemplify how targeted organizational initiatives can lead to significant productivity improvements, contributing to broader economic and developmental goals.
For more insights, read the Knowledge Management Case Studies in Mongolian Energy and Mining Sectors: https://doi.org/10.61145/JXXY1523
Source: APO Annual Report 2023